The development of modern drive trains for the automotive industry presents designers with great challenges. Increasingly complex designs and calculations are necessary to ensure that the individual components are developed to meet very specific requirements. Test stands play an important role in this area. The components used on them, such as couplings, often have to demonstrate peak performance. Coupling manufacturer R+W Antriebselemente GmbH offers a variety of solutions for these types of applications.
Rigorous tests, a wide range of high accuracy procedures and measurements, flexibility, requirements for the highest precision – test benches have to do it all. This requires efficient and reliable high performance couplings. In order to provide the right coupling for the widest possible range of test stand applications, coupling manufacturers have to take a complex patchwork of technical specifications into account during design and development. Aspects such as torque, speed, balance, stiffness, shaft misalignment, moment of inertia, and available space are just a few considerations. In one case where a leading motorcycle manufacturer called on R+W, the highest standards with regard to repeatability, control performance and system dynamics had to be met to ensure that their high performance racing engines could be reliably tested and examined on an assembly test stand. This complex undertaking required a special custom-made coupling.
Lightweight design and high-performance materials
The basic design of a racing test stand differs only slightly from that used by manufacturers of mass production vehicles, only this specific application had to handle more extreme loads with exceptional precision. A rated torque of 700 Nm had to be transmitted precisely, with zero backlash and high torsional stiffness, at up to 16,000 rpm. In order to connect the shafts and compensate for axial, lateral and angular misalignment, the coupling required a “double-flex” design that was as compact as possible. A target weight of 5kg and very high balance quality also had to be considered. The entire driveline was then to be rebalanced post-assembly, requiring that it be possible to make further changes to the mass at the pre-balanced coupling, in order to ensure that the components on the test stand worked together in harmony.
R+W’s engineers succeeded in developing a custom-made solution based on the proven LP3 series precision disc pack coupling (Image 1) that would satisfy all of the demanding requirements. Produced from high-performance materials and equipped with rotationally symmetrical conical clamping hubs, the compact and light weight coupling ensures reliable backlash free torque transmission while adhering to the required space and weight limits. In order to achieve overall accuracy, R+W also recommended and provided a special set of holes on the coupling to enable balancing weights to be installed at a later date. This allows changes to the mass to be made at the coupling during rebalancing of the complete assembly. This robust and particularly powerful new development enables the operator to put the high-performance engines through their paces and get them to the starting line.
Custom-made overload protection
Torque limiting, mechanical safety couplings represent a further use of precision couplings used in test stands. These protect drive train components, such as torque transducers and gears from torque overload and potential damage in the event of a machine crash. As a result, downtime is reduced and the availability of the system is increased.
In another example, a custom-made safety coupling turned out to be the perfect solution for an R+W customer in the automotive industry. In this application too, particular requirements regarding precision, size, torque and speed had to be considered. The result of this cooperation is an enhanced version of an R+W industrial safety coupling from the ST series (Image 2). This series has robust safety elements evenly spaced around its circumference, and is designed for especially high torque levels. This was also important for the application, since it not only had to run reliably up to a speed of 7,000 rpm, but also safely disconnect the driving and driven shafts at a disengagement torque of 2,000 Nm in case of an overload.
This customized version was designed to be more compact than the standard version, allowing it to be installed into a very tight space. As required by the application, the resulting coupling has external dimensions of only 200 mm in outside diameter and an overall length (including add-on parts) of 263 mm, with a capacity of up to 3,000 Nm at a maximum speed of 7,000 rpm. A built-in disc pack set allows the coupling system to compensate for shaft misalignment during operation. In addition to being especially compact, the design also allows for connection to various other components such as brake discs or special instrumentation. In contrast to a previously used competitor product, the additional components were included in the planning by R+W. The final product enabled the customer to eliminate adapter flanges and extra mass, while also reducing cost.
ST series industrial safety couplings are spring loaded ball-detent clutches with standard disengagement torque capacities of up to 250,000 Nm. In special versions, however, significantly higher disengagement torque levels are also possible, with virtually no limit to the torque which can be facilitated by the robust safety elements (Image 3) evenly spaced around the circumference of the coupling. In the event of a torque overload, the balls in the preloaded safety elements are forced out of their detents and cause a full and permanent disengagement between on the drive and driven components. With the aid of an additional actuation plate, which can be mounted to the back sides of the plungers, the coupling can be monitored for disengagement with a sensor or limit switch. Simple application of axial pressure to the back sides of the plungers is all that’s required to perform re-engagement after the machine is stopped. If necessary, the disengagement torque can be adjusted in just a few simple steps.
Variety, development and optimization
The R+W portfolio is as varied as customers’ individual requirements. In addition to the series described here, smaller safety couplings for torque ranges between 0.1 and 2,800 Nm, for example, are also available. Beyond safety couplings, an extremely wide variety of metal bellows couplings, elastomer couplings, gear couplings and line shafts provide users with the right solutions for a wide range of applications. With a view to future trends and ever-increasing requirements, R+W has a separate research and development department for new products and special solutions in response to customer requests. In-house static and dynamic test benches provide engineers with comprehensive options for conducting extensive product tests. R+W has the knowledge and experience to select the right coupling or line shaft to optimize all kinds of test stands – enabling companies to plan reliably and minimize cost.
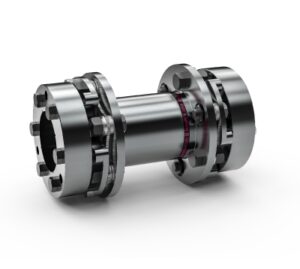
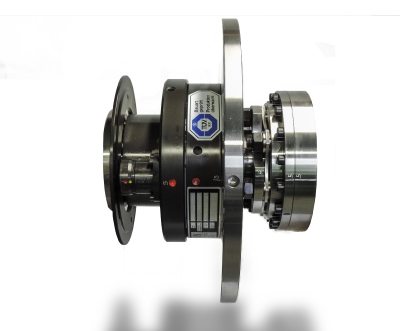
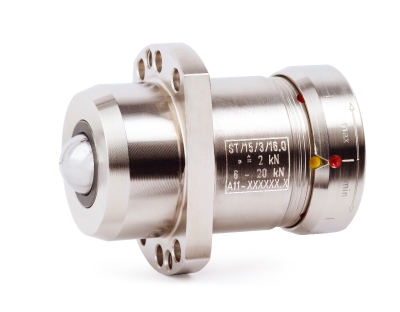