Extruder is a term commonly used in process engineering. There are two main types of extruder, categorized according to the different processes involved: processing extruders, which are normally used for shaping material, and conditioning extruders, which are used for chemical and physical modifications. During the extrusion process, a wide range of solid and liquid materials are pressed through a shaped opening under pressure. The wide range of applications also reflects the varied uses of extrusion technology in the construction, automotive, aviation, medical technology and furniture industries, to name but a few. This makes it even more important that the appropriate machine parts, including the right couplings, are selected.
The structure and function of an extruder
An extruder usually consists of a long screw shaft which fits into a barrel. The shaping outlet (die) is placed on the end of the barrel. An electric motor with a gear drive is often used to rotate the shaft and is attached to the opposite end. The materials being processed (clay, ceramic, rubber, thermoplastic polymers, dough for the food industry, aluminium, etc.) are fed into the barrel via a hopper. If additional components are needed, such as paints or strengthening materials, these are introduced via a side-feed. The barrel interior is divided into three zones in which different processes take place. In the first zone, the materials are fed in, melted and compressed. Following is the compression zone where the materials are further compacted. The discharge zone ensures that the material flows evenly to the die. Products of extrusion can include pipes, hoses, films, bicycle rims, baked goods, crispy snacks, caramel and much more – in most cases, quite a challenge for the drive system. High pressure, high temperatures and even mixing are also very important to the process. A safety coupling, which decouples in the event of a torque overload to protect expensive machine components, such as gears and shafts, makes absolute sense.
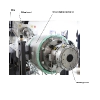
Radially mounting extruder safety coupling
The well-proven R+W ST series industrial safety couplings are available to protect many different types of extruders. These robust couplings have a compact design and have been developed specifically for high torque levels. In the event of a torque overload, which is often caused by foreign matter entering the machine, the coupling reliably disconnects the driveline in a matter of milliseconds to protect the extruder from damage. This helps to reduce significant repair costs and downtime. Once the cause of the overload has been remedied, the coupling can be quickly and easily re-engaged through axial pressure applied to the drive ball plungers. The torque limiters are designed with elastic jaw couplings in order to damp vibration and absorb shock, while simultaneously compensating for axial, angular and lateral shaft misalignment. As a result of the many different types of hub connection, such as fully split clamping collars (Figure 2 – R+W image – Safety couplings for extruders which can be mounted radially) or flange mounted keyway driven hubs, the coupling can be radially installed and removed, eliminating the difficult process of removing the motor to facilitate coupling installation. Extruder safety couplings of this specific configuration are available for disengagement torques ranging from 200 to 14,000 Nm and include optional ATEX certified versions.
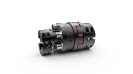
Modular design
The safety release mechanism in the coupling is made of hardened steel with a black oxide surface finish. The individual safety elements (ball-detent plungers) can be added and removed to change the disengagement torque adjustment range, and can also be adjusted within a given range. The coupling hubs and elastomer jaw sets are made of cast iron (ductile iron 40). The elastomer segments, which are the compensating elements in the elastomer coupling, are typically made from TPU or Hytrel, and are available in various Shore hardnesses, offering more flexibility to extruder applications. R+W sells elastomer inserts in Shore hardnesses of 98 Sh A (good damping) or 64 Sh D (high torsional rigidity), for example, with each type easily identifiable by color. The elastomer material is significant in terms of the properties of the coupling and the driveline as a whole, helping to optimize the torsional vibration of the system.
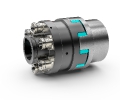
Safety element torque limiters
Because of the robust design, R+W safety element torque limiters are recommended for many demanding applications, including rolling mills and other steel mill equipment, wind power generators, excavators, water treatment plants, industrial shredders, tunnel boring machines, and extruders. Their compact, simple design and precise adjustability make them an excellent fit for use in these applications. The overall range of safety element torque limiters from R+W is available for disengagement torques from 200 to 250,000 Nm. They are made for both direct and indirect drives with fully disengaging function.
Lower torque models
Safety couplings from R+W are available in a wide variety of designs which are selected and customized if necessary following an extensive consultation in terms of the application, in particular when they will be connected to extruders. The disengagement torque or the torque to be transmitted, the connection interface, and available space are just a few of the critical factors. Precision safety couplings in the SK/ES series are suitable for applications with a lower torque (0.1 to 2,800 Nm). The connection options vary widely, including keyway drives, conical clamping ring connections, and single split and fully split clamping hubs for lateral mounting. Depending on the layout of the machine, they are also available for indirect drive arrangements with sprocket or pulley attachments. There are also a wide variety of different function systems available, including single-position, multi-position, full disengagement or load blocking. In addition, special versions are always available.
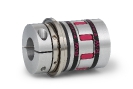
Damping and split structure
R+W Servomax® elastomer couplings also include models without an overload safety release, ranging in torque capacity from 0.5 to 25,000 Nm. The couplings are still effective for vibration damping and misalignment compensation, including easy mounting options. As stated above, a variety of insert materials and Shore hardness values are available, defining the characteristics of the complete driveline. For the connection, there are choices between the well proven keyway mounting, clamping hubs (also available in a fully split version) or conical clamping rings. In addition to being used in extruders, the fully split clamping coupling is also used on servo drives in machine tools, printing presses and packaging machines, and in control and positioning technology.
The relatively low investment in the correct coupling for valuable machine components in processing and conditioning extruders can only pay off. R+W field staff are happy to advise on extruder protection. More information can be found at www.rw-couplings.com and in the R+W app.